Extraction facility equipment requires regular maintenance and cleaning to produce an adequate yield of high-quality botanical extracts.
Quick Links
Extraction facilities are designed to process distillates on an industrial scale. Hydrocarbon extraction equipment includes vital tools for manufacturers who produce concentrates in a process that separates the plant matter from the cannabinoid-infused solvent, leaving behind only highly concentrated cannabinoids.
Extraction facilities are required to meet the same cleanliness and safety protocols as other industrial workplaces. As a result, operators have to know their extractor components intimately and understand how to clean, maintain, and repair them.
As a leading manufacturer of pressure cylinders and supplier of processed steel since the 1950s, Worthington Enterprises possesses a deep knowledge of everything from Occupational Safety and Health Administration (OSHA) regulations to employee training and safety data sheets.
Now, we’ve taken all of that deeply rooted wisdom and deployed it in Highpoint™ by Worthington Enterprises, our botanical extraction industry-focused brand of products.
In this blog, we’ll share some of that wisdom with you.
So keep reading for our top tips to maintain the cleanliness and safety of your extraction facility.
Tips for Cleaning Extraction Equipment
Not only does regular cleaning and maintenance of hydrocarbon extraction equipment keep everyone safe, but it also ensures optimal performance and maximum yields.
The medicinal and recreational botanical industries are growing—as is the demand for extracts.
Proper upkeep is crucial to maintaining a long-term foothold in the botanical extraction market. Therefore, you need to know how and when to clean, schedule maintenance, and replace certain parts.
1. Know Your Extractor Components
Knowledge is power!
When you are familiarized with hydrocarbon extraction equipment, you’ll understand the kind of care and maintenance it needs to work efficiently.
Key components of your equipment likely include extraction and separator vessels, solvent supply tanks, lines and connections, temperature controllers/chillers, and compressor pumps.
These components will inevitably become dirty or worn during the extraction process, so you should learn how each component functions and works so that you can troubleshoot as needed.
2. Determine What to Clean and When to Clean It
Organizing your cleaning and maintenance schedule helps you avoid downtime in the extraction facility.
While a good user manual will include timing recommendations and other information, your facility’s specific parameters can impact wear and tear in unique ways. This is why it’s essential to monitor your equipment and set your cleaning schedule.
In terms of what to clean, standard procedures include extraction runs without any product in the system, rinsing separator vessels and connecting lines with ethanol, and checking downstream lines/filters for any carryover debris from the extraction process.
Cleaning these components helps avoid clogged lines and valves while guarding against poor separation and an underwhelming yield.
3. Keep a Maintenance Log
Get organized!
You should keep a separate maintenance calendar for each extraction system to track cleaning schedules. Each extractor should have a logbook that documents all maintenance for easy reference.
Keeping a logbook helps you track the maintenance of your system, for example. In addition, a log of this particular maintenance should note noise level or vibration changes, indicating a potential problem in the system.
4. Always Have Extra Parts On Hand
As mentioned earlier, certain parts can become worn or even break over time. This includes valves, belts, o-rings, and consumables such as coolant, filters, and oil.
When you keep a supply of these extra parts and consumables on hand, you reduce downtime and avoid a situation where your system fails to function because of a missing element.
Anytime you can quickly fix or repair a major component of your extraction system, you minimize those moments of standing around and doing something other than extracting botanicals!
Tips for Safety in an Extraction Facility
Maintaining Safety Standards in Your Botanical Extraction Facility
Botanical extraction could potentially involve a unique set of hazards that operators must contend with to keep everyone safe.
There are flammable and combustible liquids, for starters, and supercritical fluid solvents used under high pressure. These extraction elements could pose significant risks to extraction team members.
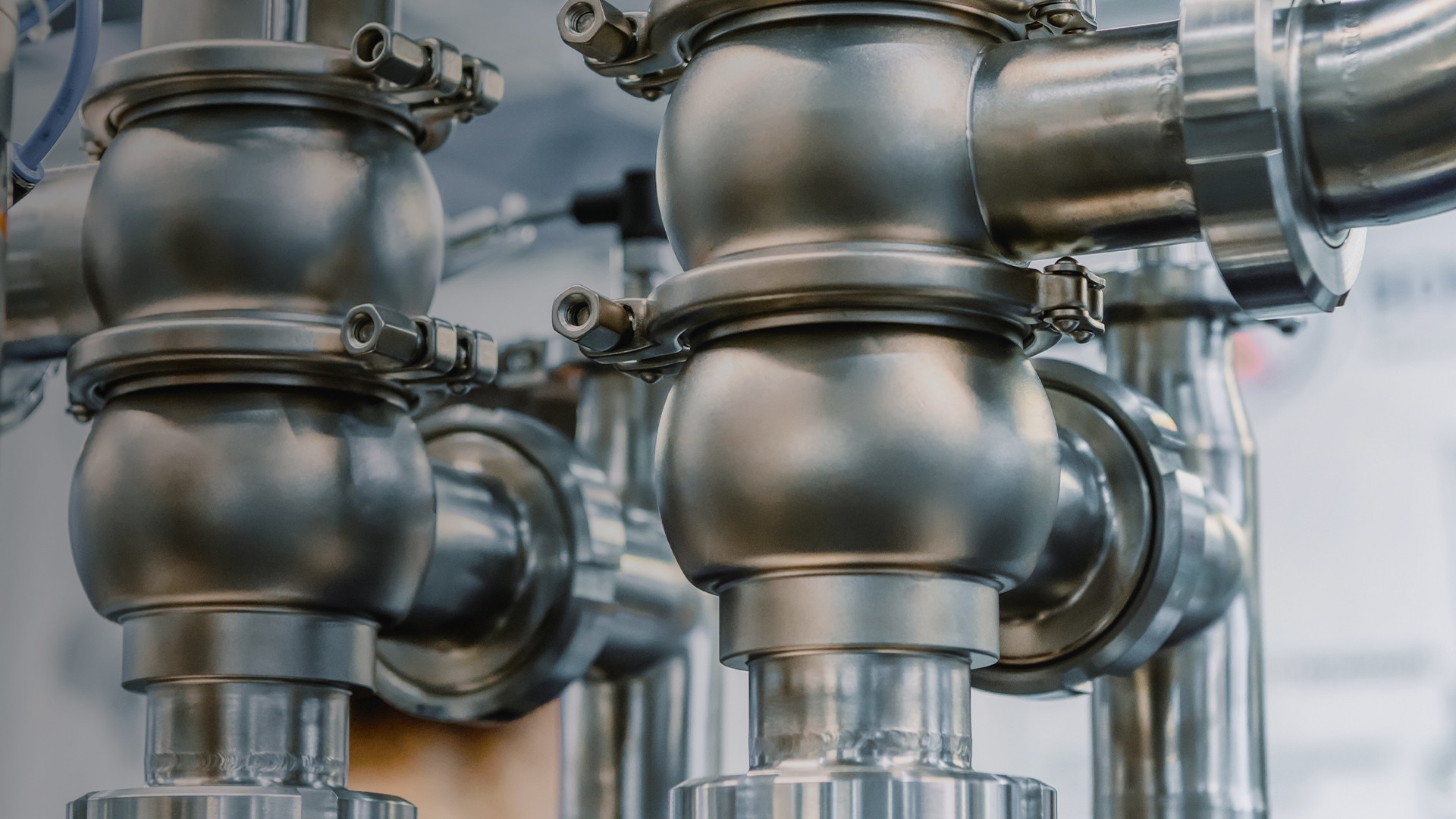
You can proactively increase worker safety with a complete Hazard Communication Program (HCP) presented by the Occupational Safety and Health Administration (OSHA).
If you maintain a workplace facility that deals with hazardous chemicals, you’re required by OSHA to implement an HCP. This implementation happens with six steps:
Step 1. Learn the Standard/Identify Responsible Staff
- Obtain a copy of OSHA’s Hazard Communication Standard.
- Become familiar with provisions.
- Make sure that someone has primary responsibility for coordinating implementation.
- Identify staff for particular activities.
Step 2. Prepare and Implement a Written Hazard Communication Program
- Prepare a written plan to indicate how hazard communication will be addressed in your facility.
- Prepare a list or inventory of all hazardous chemicals in the workplace.
Step 3. Ensure Containers are Labeled
- Keep labels on shipped containers.
- Label workplace containers where required.
Step 4. Maintain Safety Data Sheets (SDS)
- Maintain SDS for each hazardous chemical in the workplace.
- Ensure that SDS are readily accessible to employees.
Step 5. Inform and Train Employees
- Train employees on the hazardous chemicals in their work area before the initial assignment and when new hazards are introduced.
- Include the standard requirements, hazards of chemicals, appropriate protective measures, and where and how to obtain additional information.
Step 6. Evaluate and Reassess Your Program
- Review Your HCP periodically to ensure that it is still working and meeting its objectives.
- Revise your program as appropriate to address changed conditions in the workplace.
More Botanical Extraction Safety Tips
Yes, there are a lot of safety regulations involved in botanical extraction. And the simple fact that these regulations exist is reason enough to follow them closely.
Safety Regulations
- ASME B31.3
The American Society of Mechanical Engineers (ASME) B31.1 code specifies the design requirements of high-pressure pipes. In addition, code ASME B31.1 ensures your components can withstand the natural extraction processes.
- ASME BPVC Sect. V111, Div. 1
Used to calculate the thickness measurement of pressure vessels operating at pressures that exceed 15 psi (internal or external). ASME BPVC Sect. V111, Div. 1 also addresses connections and bends in pipes and reinforcement.
Safety Data Sheets
First mentioned earlier in the Safety Standards section of this article, Safety Data Sheets (SDS) are the source of detailed information on a particular hazardous chemical. Each employee must maintain copies of SDS for all hazardous chemicals in the workplace, and all SDS should be readily accessible to workers when they are in the work areas during their shifts.
Gas Detection System
Gas monitoring is another element of safety that must be the focus of any extraction facility. These systems are crucial in hydrocarbon extraction and processing labs as they prevent instances of combustion or poisoning. Gas detection systems should be easy to use and maintain, highly accurate, and versatile, functioning as part of an integrated system or as an independent monitor.
Employee Training
Employers must train employees on the hazardous chemicals in their work area before their initial assignment and when new hazards are introduced into the work area. And, it’s vital that this training is conducted in a manner and language that all employees can understand.
Extraction Booths (Also Called “Blast Rooms” or “Blast Booths”)
The newly legalized botanical extraction industry suffered from chemical process safety gaps (primarily open blasting), which led to significant hazards for employees of extraction facilities. Today, safety regulations require extractors to use “closed-loop” systems to ensure solvents are captured for reuse rather than being released into the atmosphere.
During the extraction process, you must use extraction booths (blast rooms) designed to keep employees safe while working with volatile solvents like butane, ethanol, and more.