The use of butane and propane in hydrocarbon extraction highlights the importance of strict safety protocols.
Hydrocarbon botanical extraction employs solvents like butane and propane to extract compounds from raw plant material. These volatile solvents require strict safety measures as outlined by the Occupational Safety and Health Administration (OSHA). In addition, other botanical extraction safety protocols are related to PPE, fire safety, and emergency response plans.
No matter the industry, safety should be a top priority.
But when the industry involves highly flammable solvents, the need to strictly adhere to standard safety protocols becomes even more critical.
Botanical extraction often requires facilities to employ techniques involving alcohol extraction, hydrocarbon extraction, and supercritical carbon dioxide (CO2) extraction.
Each of these methods brings unique safety concerns to the table. Therefore, large-scale botanical extract production requires extraction technicians and facility managers to have significant safeguards.
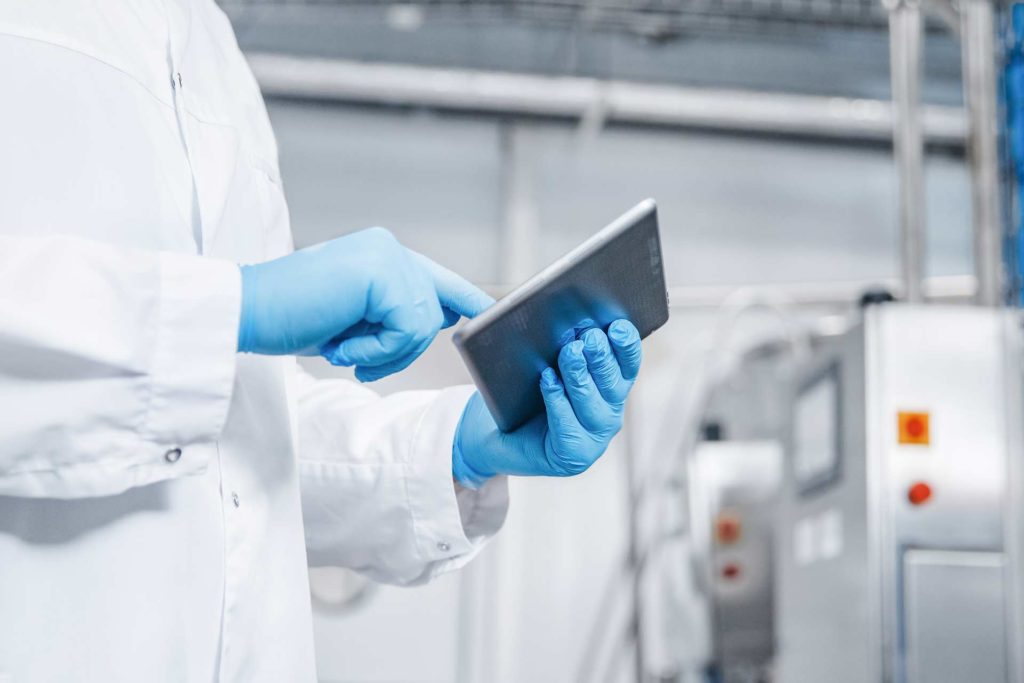
But what makes these solvents so volatile, and what are the rules for safety in hydrocarbon extraction? In this article, we’ll explain.
Botanical Extraction Techniques
As mentioned, alcohol, hydrocarbon, and CO2 are often used in botanical extraction.
Regarding safety, we’ll mainly discuss hydrocarbon (butane/propane) extraction, one of the most popular extraction methods worldwide.
Butane and propane are volatile and can be unsafe when misused. This is why professional extractors strictly follow the proper precautions.
Since butane and propane are flammable, extractors utilize closed-loop extraction systems. This ensures a safe, sealed process that locks the solvent inside the system and recovers it for future extractions.
What is Hydrocarbon Extraction?
Before diving headlong into the safety aspects, let’s first rehash the basics of hydrocarbon extraction.
Hydrocarbon extraction enlists butane or propane to separate the chemical components, the “prize” of the extraction process, from inert plant material.
After the compounds are separated from the raw plant material, the resulting extract is used to produce a wide range of concentrated botanical products.
Each piece of equipment used in hydrocarbon extraction must be up to the strict safety standards in an array of concentrations. In the next section, we will examine each of these safety components.
How to Maintain Safety in Botanical Extraction
With so many valves, tanks, lines, and pressure points to keep an eye on, ensuring safety in an extraction facility is a massive endeavor. But ultimately, it’s an endeavor you must undertake. So here are some specific areas that you can reinforce for safety.
Gas Detection System
Gas monitoring is an element of safety that must be the focus of any botanical extraction facility.
These systems are crucial in extraction and processing labs as they work to prevent instances of combustion or poisoning. A reliable gas detection system should be easy to use and maintain, highly accurate, and versatile, functioning as part of an integrated system or independent monitor.
Cylinder Connections
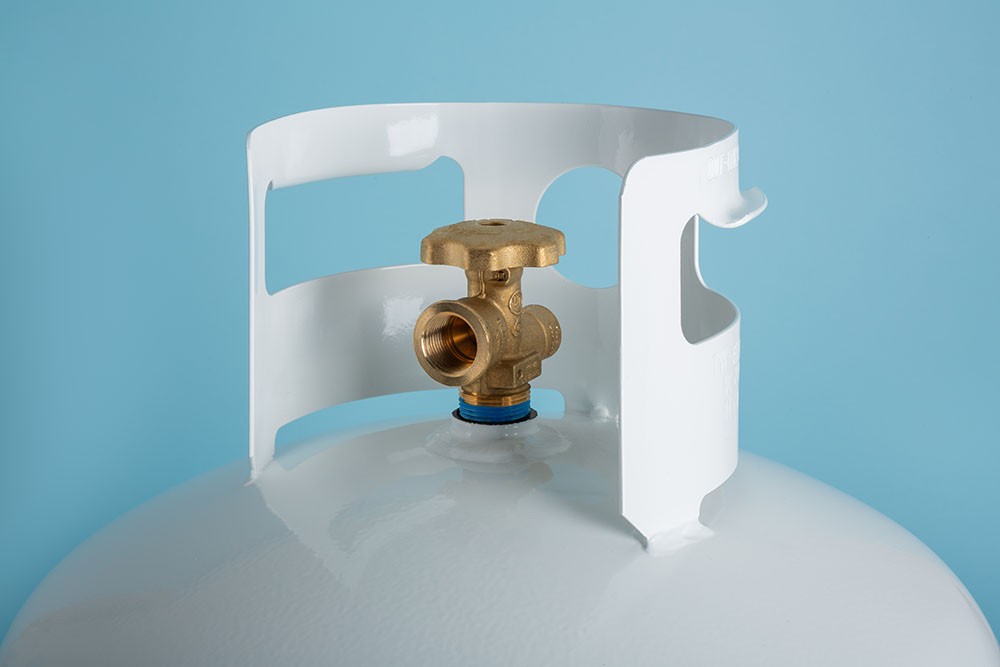
When employing butane and propane mixtures in extraction, specific cylinder connections must be used for liquid withdrawal and gas (vapor) withdrawal.
The correct cylinder connections must be used to prevent safety hazards. If incorrect connections are used, the hydrocarbon process can result in backflow contamination of oils into the cylinder, which can create problems if the cylinder is used in a different application after the next fill.
- CGA connection number 555—Liquid withdrawal
- In CGA V-1, Standard for Compressed Gas Cylinder Valve Outlet and Inlet Connections, cylinder valve outlet connection number 555 is the specified valve outlet connection for liquid withdrawal.
- CGA connection number 510—Gas (vapor) withdrawal
- In CGA V-1, cylinder valve outlet connection number 510 is the specified valve outlet connection for gas (vapor) withdrawal.
Static Electricity
Botanical extraction sees liquids being transferred from one metal container to another. This could result in static electrical sparks.
To prevent the build-up of static electricity and sparks from causing a fire, it’s vital to bond metal dispensing and receiving containers together before pouring.
Bonding is done by making an electrical connection from one metal container to the other. This ensures that there will be no difference in electrical potential between the two containers and, therefore, no sparks will form.
Additionally, many extractors use electrostatic discharge (ESD) flooring which is an ideal solution in facilities and industries requiring antistatic environments (like botanical hydrocarbon extraction).
Storage and Dispensing (Hydrocarbon Storage Tanks)
Hydrocarbon storage tanks and other large vessels require special equipment to keep products viable and team members safe. Such equipment includes flame arrestors, emergency relief vents, tank blanketing valves, and pressure vacuum relief valves.
- Flame Arrestors: This allows gas and vapor to pass through but stops fuel combustion by extinguishing the flame.
- Tank Blanketing Valves: Applies a blanket of an inert gas (nitrogen) in the vapor space above the liquid in a closed storage tank.
- Emergency Relief Vents: Provides emergency venting from abnormal internal pressure, preventing a fire from burning around the tank.
- Pressure Vacuum Relief Valves: Controls the pressure in a system or vessel, which can build up because of an instrument, equipment failure, or fire.
Separation Distances — Class 1, Division 1 (C1D1)
Botanical extraction must occur in a C1D1 (Class 1 Division 1) compliant environment. The safeguards inherent in C1D1 extraction booths are necessary to prevent fires, explosions, damage to products, and human injuries.
C1D1 extraction room equipment includes:
- Emergency Lighting
- Cameras for Remote Monitoring
- LED and Dimmable Lights
- Hood Lights
- Ventilation Fans
- Outlets and Switches
- Exit Signs
The quickest—and the safest—way to get all of the C1D1 features you need in your facility is a prefab C1D1 extraction room. Also known as an extraction booth, these units can be built and installed in one day.
They should be compliant with local codes and regulations. These units include purge systems, exhaust systems, a gas detection kit, and a bevy of other features that makes the unit compliant with most regulations, including OSHA Safety and Health Standards (more on OSHA later in the article).
Hazard Communication
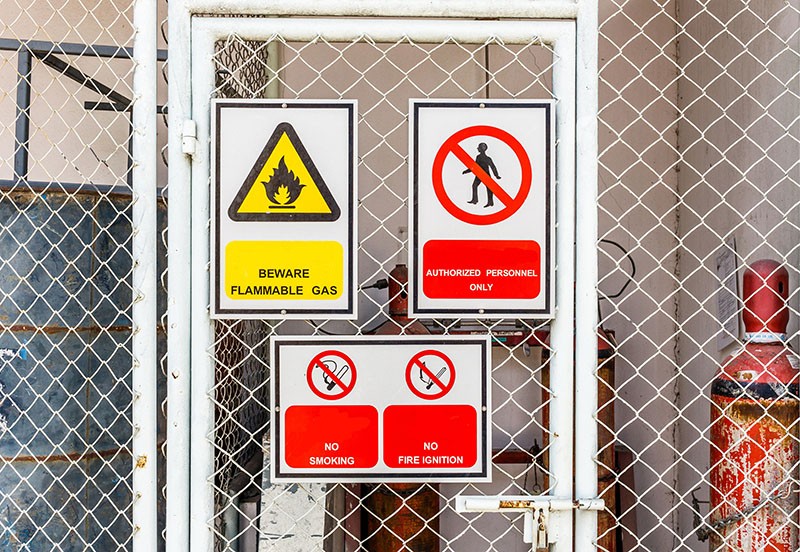
Hazard communication, also known as HazCom, is a set of processes and procedures that employers and importers must implement in extraction facilities to effectively communicate hazards associated with chemicals during handling and shipping and any form of exposure.
To ensure chemical safety in extraction facilities, information about the hazards of chemicals must be available and understandable to all team members participating in the extraction process.
OSHA’s Hazard Communication Standard (HCS) requires the development and dissemination of info such as:
- Chemical manufacturers and importers must evaluate the hazards of the chemicals they produce or import and prepare labels and safety data sheets to convey the hazard information to their downstream customers.
- All employers with hazardous chemicals in their workplaces must have labels and safety data sheets for their exposed workers and train them to handle the chemicals appropriately.
Personal Protective Equipment (PPE) for Extraction Facilities
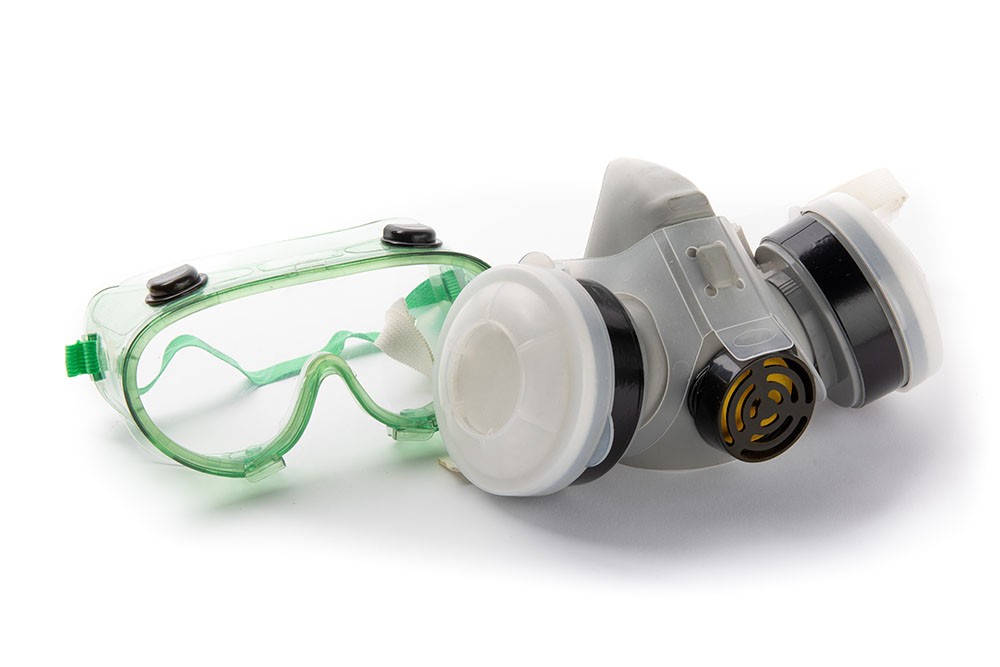
Utilizing personal protective equipment (PPE) that’s well-fitted, cleaned, and properly maintained is a must during all stages of production. PPE significantly reduces the risk of exposure to numerous hazards while preventing serious injury.
Proper PPE for extractors includes:
- Gloves: Should fit tightly and be oil and puncture-resistant. Disposable nitrile gloves are recommended.
- Safety goggles: Protect eyes from chemical splashes and flying debris. Varieties include direct vented goggles, indirect vented goggles, and non-vented goggles.
- Respirator: Half-face respirators covering the mouth and nose can provide respiratory protection from fine particulates.
- Lab coats: They should be fire-resistant, anti-static, and grounded, with plenty of room for storage. When handling liquid chemicals, latex or nitrile chemical aprons are recommended.
Emergency Response Plan
The actions you take in the first few minutes of an emergency are crucial to the safety of everyone in your extraction facility.
To develop a comprehensive Emergency Response Plan (ERP), you must first conduct a risk assessment to identify exactly what could go wrong in an extraction facility. Understanding this can help determine resource requirements and help your facility prepare for emergencies.
NFPA Fire Code (NFPA 58)
One of the chief concerns of any processing or manufacturing facility is the threat of fire. This is especially true in botanical extraction facilities, especially those utilizing hydrocarbon solvents.
The National Fire Protection Association Fire Code (NFPA 58) focuses on controlling Liquefied Petroleum Gas (LPG) risk, acting as the industry benchmark for safe storage, handling, transportation, and use.
The NFPA 58 “mitigates risks and ensures safe installations, to prevent failures, leaks, and tampering that could lead to fires and explosions.”
According to the NFPA 58 Fire Safety Analysis, the following fire protection improvements are recommended:
- Install automatic shutoff protection through thermal (fire) sensitive elements in the valve or valve actuation release elements within 5 feet of the end of the hose or swivel piping connected to the line at the truck loading rack for LPG.
- Install automatic shutoff protection through thermal (fire) sensitive elements in the valve or valve actuation release elements on emergency shutoff valves on the LPG storage vessels.
- Share the completed fire safety analysis with the jurisdiction authority and local emergency responders.
Expanded Safety in Hydrocarbon Extraction
Botanical extraction could potentially involve a unique set of hazards that operators must contend with to keep everyone safe.
There are flammable and combustible liquids, for starters, and supercritical fluid solvents used under high pressure. These extraction elements could pose significant risks to extraction team members.
You can proactively increase worker safety with a complete Hazard Communication Program (HCP) presented by the Occupational Safety and Health Administration (OSHA).
If you maintain a workplace facility that deals with hazardous chemicals, you’re required by OSHA to implement an HCP. This implementation happens with six steps:
Step 1. Learn the Standard/Identify Responsible Staff
- Obtain a copy of OSHA’s Hazard Communication Standard.
- Become familiar with provisions.
- Make sure that someone has primary responsibility for coordinating implementation.
- Identify staff for particular activities.
Step 2. Prepare and Implement a Written Hazard Communication Program
- Prepare a written plan to indicate how hazard communication will be addressed in your facility.
- Prepare a list or inventory of all hazardous chemicals in the workplace.
Step 3. Ensure Containers are Labeled
- Keep labels on shipped containers.
- Label workplace containers where required.
Step 4. Maintain Safety Data Sheets (SDS)
- Maintain SDS for each hazardous chemical in the workplace.
- Ensure that SDS are readily accessible to employees.
Step 5. Inform and Train Employees
- Train employees on the hazardous chemicals in their work area before the initial assignment and when new hazards are introduced.
- Include the requirements of the standard, hazards of chemicals, appropriate protective measures, and where and how to obtain additional information.
Step 6. Evaluate and Reassess Your Program
- Review Your HCP periodically to ensure it is still working and meeting its objectives.
- Revise your program as appropriate to address changed conditions in the workplace.
More Tips for Safety in Botanical Extraction
Safety protocols don’t end at OSHA and a rock-solid HCP.
Safety regulations are also explicitly related to engineers—the pros working in botanical extraction facilities. These vital regulations include:
- ASME B31.3
- The American Society of Mechanical Engineers (ASME) B31.1 code specifies the design requirements of high-pressure pipes. Code ASME B31.1 ensures your components can withstand the natural processes of THC extraction.
- ASME BPVC Sect. V111, Div. 1
- Used to calculate the thickness measurement of pressure vessels operating at pressures that exceed 15 psi (internal or external). ASME BPVC Sect. V111, Div. 1 also addresses connections and bends in pipes and reinforcement.
A High Standard for Safety in Extraction Equipment
As a manufacturer of stainless and carbon steel tanks and other related metal-based equipment since the 1950s, Worthington Enterprises has intimate knowledge of everything from OSHA regulations to fire safety to PPE.
That deeply rooted wisdom is now deployed in Highpoint™ by Worthington Enterprises, our botanical extraction-focused products.
Let’s elevate the process. Click here to start your Highpoint journey.
*Highpoint by Worthington Enterprises are not extractors. As such, you should not consider the information contained in this blog advice or instruction. We strongly suggest you reach out to the proper licensing and certification authorities to ensure you operate safely and compliantly.